To offer new solutions for product handling and end of line packaging – that was SOMIC’s claim at the Interpack 2023 in Duesseldorf in May. The specialists for end of line packaging from Amerang in Upper Bavaria presented two exciting solutions that will make their company’s portfolio fit for the future.
In this interview, Managing Director Patrick Bonetsmüller, Ralf Jäckel, Director of Sales Europe, and Josef Bliemel, Director of Systems Engineering, explain the new systems’ innovations and the benefits these solutions provide to users in the field.
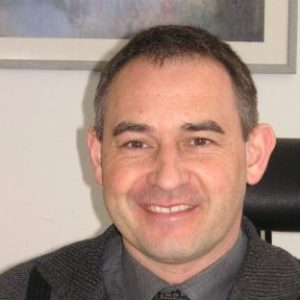
Q: Mr. Bonetsmüller, can you elaborate on the background of these new SOMIC solutions?
Patrick Bonetsmüller: We can see logical advancements of the SOMIC machine concept here, which make our machines fit for future needs. As shareholders, we naturally keep an eye on market developments and recognize the demands that are placed on our machines in the field. Therefore, we tasked our development team with the following global challenge: “We want to position our machines with an eye to the future.” This was deliberately kept open to avoid limiting the creativity in our teams from the outset, and – as you can see – it worked very well. Today, we are looking at two completely new systems: An additional solution for flexible product handling with our CORAS collection and sorting system as well as the new SOMIC 434 machine generation.
Q: Mr. Bliemel, you bundled all the requirements that were to be integrated into the new machine. Can you give us an overview in that regard?
Josef Bliemel: For the new 434 machine series, we first brought all the issues to the table that were expressed in conversations with customers. For example, we have often seen the request for the end of line packaging machine to be integrated into the linear arrangement of a packaging line. In this respect, we were occasionally limited with the predecessor machine and the previous concept. That is why you now see the new machine here, which lines up all modules from the carton infeed to the delivery of the filled and closed cartons in a linear arrangement. This leads to a somewhat slimmer frame width and to the bundling of all cable ducts. As a result, we can ensure a high level of hygiene and easy accessibility of the cables during maintenance activities. Hygiene also includes the fact that we now set up the machine on a stainless-steel frame construction. This was another request from several customers that we picked up from the market.
Q: Mr. Jäckel, you have now presented the new machine to your customers at the trade show. What kind of feedback do you take away?
Ralf Jäckel: In the new design, we have also integrated several elements for even greater ease of use. Of course, this is very well received because it reduces the workload of the operators, who, after all, are confronted with a wide range of tasks in the packaging operation. Our customers have been very positive about the largely automated format change, which we achieve with the aid of servomotors. The adjustment of folding tools, gluing positions, and blank magazines as well as the subsequent change of individual format parts with our QuickChange system can now be carried out considerably faster, with time savings of up to 70%. For our customers, this is a major advantage when they consider the variety of formats in their product portfolio. This played a significant role in many conversations here at the trade show. Patrick Bonetsmüller: Customers have also responded very positively to the modular machine concept, since it offers the option of adapting the end of line packaging machine if there are changes in the product range. The decision in favor of a SOMIC 434 thus represents a future-proof investment for our customers.
Q: Mr. Bliemel, the machine also differs from the previous concept of a SOMIC machine in other aspects. Which points are particularly important here?
Josef Bliemel: The improvements pay off overall in terms of operator comfort. This involves the format change – as already mentioned – but also the overall accessibility of the machine. We have moved the support structure of the frame that holds the functional groups to the inside, which enables virtually unimpeded access to the machine’s interior. In addition, we have redesigned the machine doors so that they can be opened by 180 degrees. This is an important aspect considering the limited space in the packaging line. And another eye-catcher here at the trade show was without a doubt the LED lighting, which adds a futuristic touch. Yet, this also has an important benefit for the operator. The machine status is now even more visible from all positions in a packaging line.
Q: Could we briefly highlight the second innovation at your booth as well?
Patrick Bonetsmüller: Here, you can see our new CORAS collection and grouping system, which takes product infeed into the packaging machine to an entirely new level. We can accept products from a variable number of lines, orient them in any way with the help of carriers and transfer them to the packaging machine in the arrangement desired by the user. For this purpose, our developers use the planar drive system technology, allowing us to offer unprecedented flexibility in product arrangement. In the process, the products are always fixed and the group can thus be transferred in its entirety to the cartoning.
Q: What performance can be achieved with this system?
Ralf Jäckel: Here, we show our customers the system connected to four lines, which allows us to collect 240 products per minute. This means that even multiple products can be taken from the lines with one carrier and transferred to the packaging machine.
Q: What is the strategic thinking behind this innovation, Mr. Bonetsmüller?
Patrick Bonetsmüller: The demands on the flexibility of a packaging line are constantly increasing. At the same time, the variety of products is increasing and retailers’ requests for any desired combination of product variants are by now a must for food manufacturers or the makers of cosmetics, non-food, or pet-food products. To reflect this in the traditional collection and grouping strategy was only possible with a great deal of technical and spatial effort. That is why we charged our developers with the task of implementing product handling and product alignment in a single concept. The planar technology, the unlimited programmability of the floating carriers and the arbitrary arrangement of the products, including a rotation of 360 degrees along the vertical axis, ensure precisely this flexibility for our customers in the future. Q: How has the system been received here at the trade show thus far? Patrick Bonetsmüller: We have had some very interesting conversations. All visitors to our booth responded extremely positively to this solution. Mr. Bonetsmüller, Mr. Bliemel and Mr. Jäckel, thank you very much for these insights into SOMIC’s trade fair news.